UDMpa
1,2 drives, 12-60Vdc or 12-100Vdc, up to 13.3/40A
EtherCAT® Dual & Single Axis Module
Powerful & Smart EtherCAT Drive Module
- Two drives per module for Gantry control
- Voltage: 12-60Vdc or 12-100Vdc
- Current: Up to 13.3A / 40A (cont./peak)
Uncompromised speed and resolution
- 2 Analog Sin-Cos 1Vptp encoders with frequency up to 500KHz
- Encoder multiplication of 4 to 4,096
- Automatic encoder offsets and gain compensation and error detection
- Dual feedback support
- Optional internal relays for dynamic braking (shorting motor phases)
Smart Motion related I/O
- 4 encoder registration MARK inputs
- 2 Position Event Generator (PEG) outputs
- 2 motor brake / relay outputs
- 2 analog inputs, 12 bit resolution, ±10V or 0-10V
- 2 analog outputs, 10 bit resolution, ±10V
- Safe Torque Off (STO)
The UDMPA is a line of economical and compact EtherCAT® drive modules. |
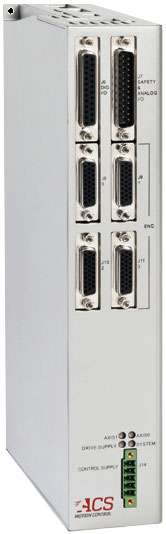 |
The UDMPA is specifically designed to complement the highest performance NPMPM drives and address the needs
for a more economical drives. It has the same form factor as the NPMPM and same connectivity.
The UDMPA is a slave that runs under any ACS EtherCAT® masters.
A comprehensive set of software support tools are provided for module configuration, setup and tuning.
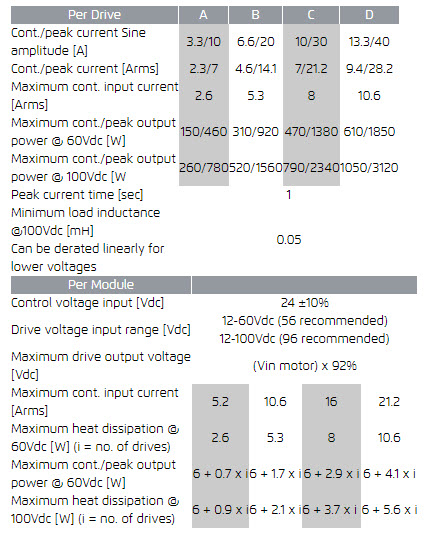
Drives
Type: digital current control with field oriented control and space vector modulation.
Current ripple frequency: 40 kHz
Current loop sampling rate: 20 kHz
Programmable Current loop bandwidth: up to 5 kHz
Commutation type: sinusoidal. Initialization with or without hall sensors
Switching method: advanced unipolar PWM
Built-in relays short motor phases upon disable (16A nominal, for dynamic braking).
Protection: Over & under voltage, Over current, Over temperature,Phase to phase and phase to ground short (short circuit on one of the motor phases might damage the drive).
Supply
The module is fed by two power sources. A motor supply and a 24Vdc control supply. During emergency conditions there is no need to remove the 24Vdc control supply. (If STO is used, then there is also no need to remove th motor supply)..
Motor Drive Supply
Range: 12Vdc to 60Vdc or 12Vdc to 100Vdc,
Recommended range: 12-56Vdc for 60Vdc version, 12-96Vdc for 100Vdc version.
Current rating should be calculated based on actual load.
If regeneration resistor is required, it should be added in parallel to motor supply with activation at 62V for 60V version or 102V for the 100V version.
Control Supply
Range: 24Vdc ± 10%.
Maximum input current / power: 0.9A @21.6V/ 20W Without motor brakes.
With 2 motor brakes: 1.9A @ 21.6Vdc / 42W
Built-in motor phases shortening relays.
Protection: reverse polarity. A 3A external fuse must be used.
Motor Type
Two- and three-phase permanent magnet synchronous (DC brushless/AC servo), DC brush, Voice coil, Two- and three-phase stepper (micro-stepping open or closed loop).
Feedback
Types: Incremental digital encoders (AqB), Hall inputs, analog Sin-Cos
(optional).
Incremental Digital Encoder: One per axis. A&B,I and Clk/Dir, Type:
Differential RS-422. Max. rate: 50M quad counts/sec.
Protection: Encoder error, not connected.
Sin-Cos Analog Encoder: One per axis.
Type: 1Vptp, differential.
Programmable multiplication factor: x4 to 4,096.
Maximum frequency: 500kHz.
Maximum acceleration with Sin-Cos encoder: 108 sine periods/second2.
Absolute Encoder (optional): EnDat 2.2 & 2.1(digital only), Biss-A/B/C.
Hall inputs: A set of three per axis.
Type: single-ended, 5V, source, open cathode. Input current: <7mA.
Feedback supplies: For all digital feedback devices: 5V, 0.5A.
For all analog feedback devices: 5V, 1.5A.
Digital I/O
For different I/O configurations see ordering options
Safety Inputs: Left & right limit inputs per axis.
Type: 24V/ source (default), single ended, opto-isolated. Input current 4-14mA.
STO: Two inputs, 24V ±20%. Input current: <50mA
All drives are disabled within 200mS
Registration Mark Inputs: (High Speed Position Capture): Four, 24V±20%,
opto-isolated, two terminals. Input current 4-14mA.
Can be used as general purpose inputs.
General purpose output: Motor Mechanical Brake output: Two, 5/24V±20%,
opto-isolated, single-ended, sink/source, 0.1A.
External Motor relay control: Two, 24V ±20%, source, 0.5A.
These outputs are used to shorten the phases of the motors by external
relays (if the optional internal relays are not present).
PEG (Position Event Generator): Two, Pulse or State, Differential, RS422.
Pulse width: 26nSec to 1.75mSec. Maximum
Analog I/O
Analog Inputs: Two, ±10V, differential, 12 bit resolution.
Max. input frequency: 1KHz. Offset: < 100mV
Analog Outputs: Two, ±10V, differential, 10 bit resolution.
Offset: ±100mV, Bandwidth: 5KHz. Max. output load: 10KΩ,
Noise / Ripple: < 25mV.
EtherCAT Communication
Two ports, In and Out, RJ45 connector
Environment
Operating range: 0 to + 40°C
Storage and transportation range: -25 to +60°C
Humidity (operating range): 5% to 90% non-condensing
Dimensions
257x154.9x50.9 mm3
Weight:
1.6 Kg.
Accessories
UDMpa-ACC1: Mating Connector Kit
UDMpa-ACC2: UDMpa (J1) mating 2m flying lead cable
STO-ACC1: 2 meter cable with flying leads
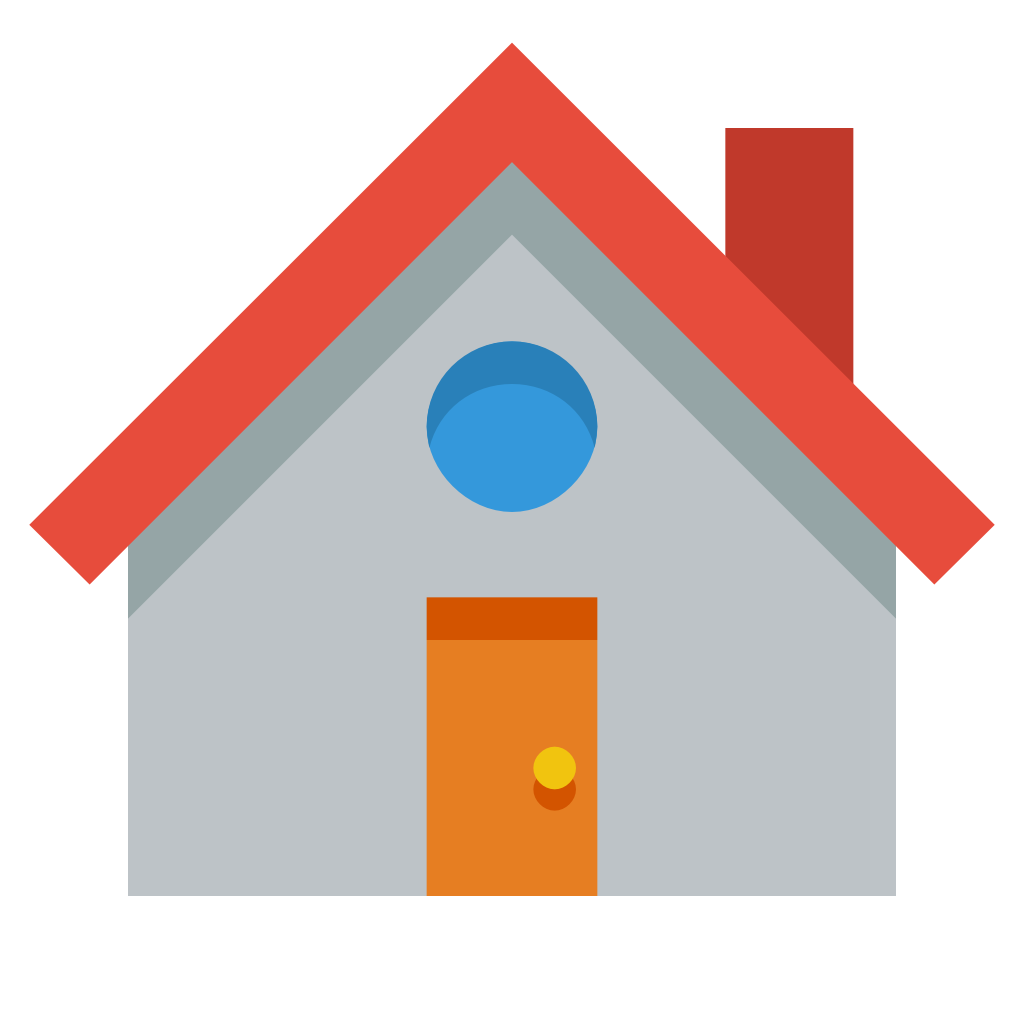
|